Case Study
Custom Job Costing Software for Precision Manufacturer
SE MICHIGAN Steel Pipe and Tubes Manufacturer employs a staff of approximately 10 to 19. Their business process was pen and paper with spreadsheets. We created a custom software for Steel Pipe and Tubes Manufacturing that automated their spreadsheets, data, and business process so they can instantly see their margins, costs, labor hours, and where they can save. They’ve used this data to advertise towards more profitable jobs. They now have a proprietary edge over their competition, their process is quicker than ever, and they are making more profit by focusing on what they are best at.
Our business analyst worked one on one with the end-user employees to define their business process so we can narrow our objective. We presented the business owners with a custom software project that would track their job costing and add features from there. After testing and training the employees saved a lot of time on data entry and spreadsheets. Employees are able to log-in to their own profile and enter information about clients, vendors, production, inventory, and even timecards. They are able to instantly see their margins on every job and change their process to reduce cost in wasted labor hours, computer downtime, and which clients to go after. They own the software and are free to update or license it themselves, and they have saved hundreds of thousands on monthly subscriptions to “canned” software.
The future is bright for this manufacturer, they are making more profit per job with the same employees. Employees are happy because the system functions well and they got say in the design. They are doing more production than ever, with less downtime.
If your business is using an “old school” process and you’re looking to benefit from software without monthly fees contact us. We can build you a custom software that does exactly what you need, that you own.
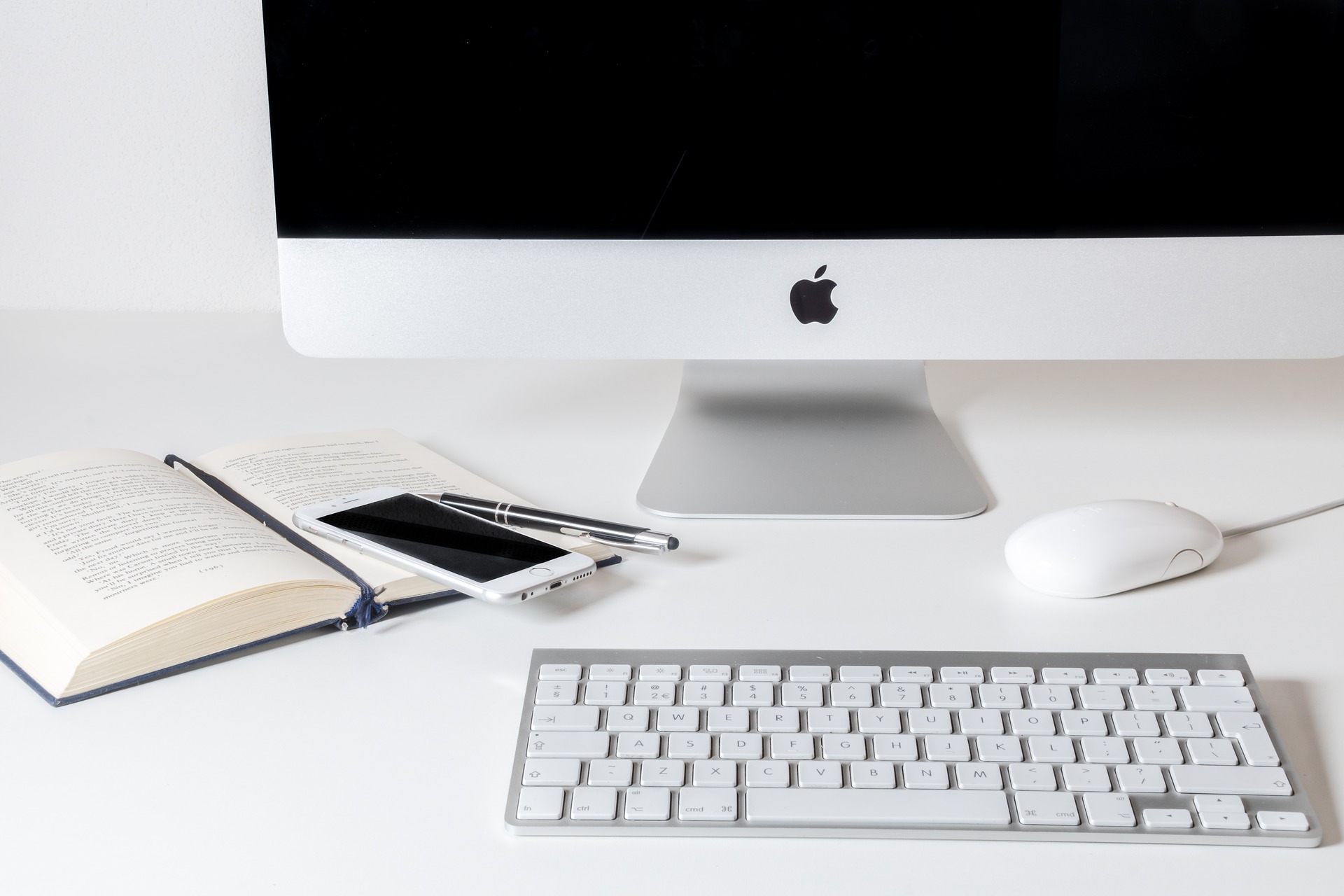